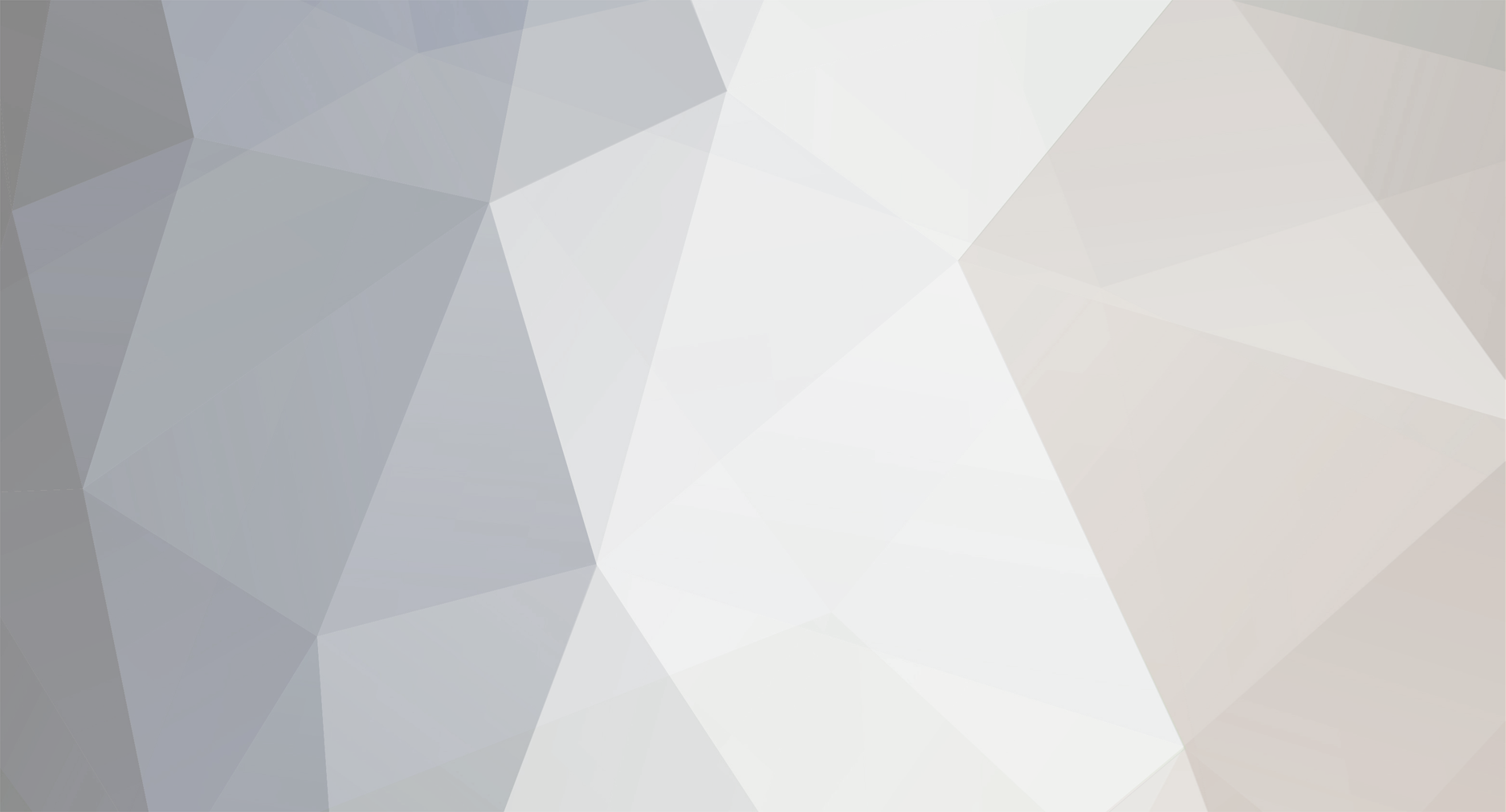
knights_templar
Community user-
Posts
1,215 -
Joined
-
Last visited
-
Days Won
5
Content Type
Profiles
Forums
Events
Store
Community Map
Everything posted by knights_templar
-
I think you are right when you say "There seem to be mixed opinions but I was wondering are there any serious disadvantages to getting an MOT before the IVA?" I think the problem lies in the perception of what an MOT is or does. The MOT test checks a vehicle against a series of standards, one being vehicle emission, those standards do have some comparisons with the IVA, but they are not the same. The IVA is looking at a vehicle in terms of build, safety and legal standards, which the MOT assumes some of these are already met because the vehicle is registered. An MOT tester will check the rear fog light works, an IVA tester will check it works with dip beam headlights only, is at the correct angle and within the specified positioning, has the correct lens identification has the correct radius on the edges etc. etc. The MOT procedure, can be carried out on anything, however until IVA'd and registered the vehicle does not appear on the MOT database so the test procedure can not be recorded. There is also no information as to which standard of emission the vehicle should be tested too. It can be manually set in the test machine and most engines are going to be post 1996 so under current standards, but pre 1996 could be age related or current depending on the proof of age. Its value is in that it is a second pair of eye being cast over your build, and they have the equipment to accurately test the emissions, something that most garages could do MOT testing or not.
-
Could you give us the information on the details screen of the ECU software. If you do not know the software, have you got internet connection near the car?
-
Fitting mini wiper motor to ford Sierra stalks
knights_templar replied to a topic in Fitting & bodywork
you will need to join the two -
Fitting mini wiper motor to ford Sierra stalks
knights_templar replied to a topic in Fitting & bodywork
Motor files is to big, it will not let me upload, so link https://www.dropbox.com/s/v26mprataahv2ix/040_151.jpg?dl=0 -
Fitting mini wiper motor to ford Sierra stalks
knights_templar replied to a topic in Fitting & bodywork
Switch GBS_Workshop_Manual.pdf -
ATR throttles and GBS map? Connect your computer to the ECU, check the details screen. what does it say?
-
the SAE rating advised by the engine manufacturer. make of oil is unimportant, unless the engine needs adertives as descrided by the DIN rating or for some manufactuers the JAP rating
-
The p&p loom is bench tested before going to GBS so unless you have worked on anything it should work. That said the loom terminals can pull off wires if the pulgs are jarred during fitting. More likely something you have touched is not quite right, same as others have said, back to basics. TPS wiring, on the ATR the TPS is not, or wasn't P&P, check the wiring, it is easy to get wrong. https://www.dropbox.com/s/20z02p6f5bbl8dl/TPS plug.pdf?dl=0 I think someone has already mentioned the crank sensor change if the engine was originally auto, flywheel bolt pattern is off set so should only be possible to fit one way. Coil pack to plugs as discussed by others, as previously mentioned the Zetec plugs are prone to fouling. TPS calibration, also check that the TPS reading rises smoothly as you operate the throttle. A reverse reading, or a stepped readout can mean wiring issues or a faulty TPS. Second the throttle basic set up, the ATR's are not calibrated from factory, so you must check as I mentioned in previous post, I can post the ATR setup procedure but it needs the engine running first.
-
the zetec map on the ECU should get you started, However it will not be ideal. you will need a RR session. Have you calibrated TPS? this procedure needs to be done frequently when setting up. Identify the master throttle, that is the one controlled by the tickover screw. most likly the rear most throttle, cylinder number 4, (forth from front) Check TPS readout, unless you are using the Ford unit, the aftermarket ones can be iffy, to say the least, you need a smooth signal change when you operate the throttle, if it steps you have it wired wrong, or a faulty TPS Where are your throttles set? make sure they are all closed, 1 (master) and its partner No2 are joined so can only be balanced with the air bleeds, No1 and No 3 should be at the same throttle position, No 3 is paired with 4 so same as 1 and 2 Make sure the air bleeds fully shut. make sure 1 and 3 are just open, visually, the same amount. you may need to adjust the link between the 1&2 and the 3&4 to match 3 to 1 if it then starts you will have to fine the start of the map, I wrote a procedure for Jenvey and Plenhum, but its the same principle. If it does not start, be very carful testing sparks, approx 25000 volts will find the easiest way to earth, if thats through the ECU, bye bye ECU trigger circuit, seen it a few times. Zetec plugs are also very prone to enameling, so have another set ready and be prepaired to swap, plug at a time to test they are OK Is this making sence, or am I rambling?
-
Check the steering lock boltit sits under the steering shaft and slides out when the key is witdrawn. for security it has to be in the withdrawn position to allow the wheel to be removed, if it is is in the locked position when you try and fit the wheel the bolt is pushed back jamming it. the bolt is operated from a cam behind the lock operating the bolt by a lever, if the bolt is jammed the switch does not turn. Cant find any pic at present, but to be honest my files are all over the place, stored on differnt cloud sites, am trying to assemble in one place.
-
The Aux plug indicator connections simply allow options, if you have the Ford switches, and the P&P adaptor you have all you need for indicators and hazards. If you want a centre Hazard switch or a remote indicator switch there is provision in the aux plug
-
You must make sure the the key is turned to the ignition position when fitting the steering wheel. best to disconnect the battery as it may take some time and some ignition setups will overheat the coil/coils. If you have tightened the wheel with ignition off, it is possible you have pushed the steering lock bolt out of position, with wheel off, check the bolt withdraws when you turn the ignition on and drops when you remove the key. It is possible to get the bolt working again if you tap th bolt in the right place.
-
If its the small alternator that GBS use on the Zetec, a resistor should not be neccesary. How have you wired the LED? should be + ignition live to + of LED, - of LED to alternator.
-
As Andi says, lift a wheel and rotate axle stand witha screw driver on top can be used as a fixed point. move fixed point to various points on the tyre and visually check tyre wheel etc for run out, you can remove wheel and do the same on disc and hub. Not accurate, you neeed a dial gauge for that but it is usually accurate enough.
-
The design has not changed, other than the donor, and the Zero does not normaly suffer from judder when braking. Check your brakes, hubs, wheels for run out and balance.
-
With that kit you will have a post 1996 emission requirement, removing the CAT will have no benefit just a problem of trying to achieve post 1996 with kit designed for when emissions were of no interest. Why are you considering this?
-
There is no wiring diagram for the GBS p&P loom, there is a diagram for the early Zero, based on the Vicky green loom If you need info on the P&P I would go to the GBS forum, I can help with specifics from there.
-
standard early type or standard late type with large cylinder? If later type does it have the built in CAT?
-
its a specially made cable for GBS https://www.kitspares.co.uk/index.php?route=product/product&keyword=clutch+cable&product_id=306
-
MAP is not used in basic plenum setup, just air temp and TPS. iacv also adds more complexity, it is not switched on in any of the maps, its not difficult.
-
Parallel, I assume Ford setup.
-
I have never seen overheating on a black top in a zero unless the basic rules have not been followed. Some filler caps have problems dealing to the rough cast alloy of some water rails, drilling holes in the state can aid filling and bleeding, but is no use to overcome overheating, the stat temp is important, if the water rails came from GBS it should be right, but have change them from other suppliers. If your system uses cooling fan switch and not ECU I would agree that you need to check operation and position in the cooling system. Getting all the air out of the cooling system is important. There is a written procedure to do this, or air gets trapped in the water rail and top hose, if that is where the fan sensor double problem.
-
There is a cooling system bleed procedure you should follow, had that been done? Smith's gauges are notoriously inaccurate, have you checked what the ECU is seeing, and is the fan set to cut in at 98 deg? Is the piping from the GBS type?
-
On the standard Ford alternator you will need a resistor between 12v + ignition and battery field wire, the small diameter wire, with led light in parallel, as above ignition 12+ to + of led - to alternator field wire.
-
Links go dead to avoid builders misreading posts and assuming they are relevant to their build. ask a question and the answer, specific to your build, can be re posted. There are three looms that could be used on the Zero, one being the P&P, and there are two sub versions of that. plus the Mazda. So is the info from across the pond correct? Well yes, unless the aux plug has one of my mods, and it does not look like it, That is what I put in the manual.