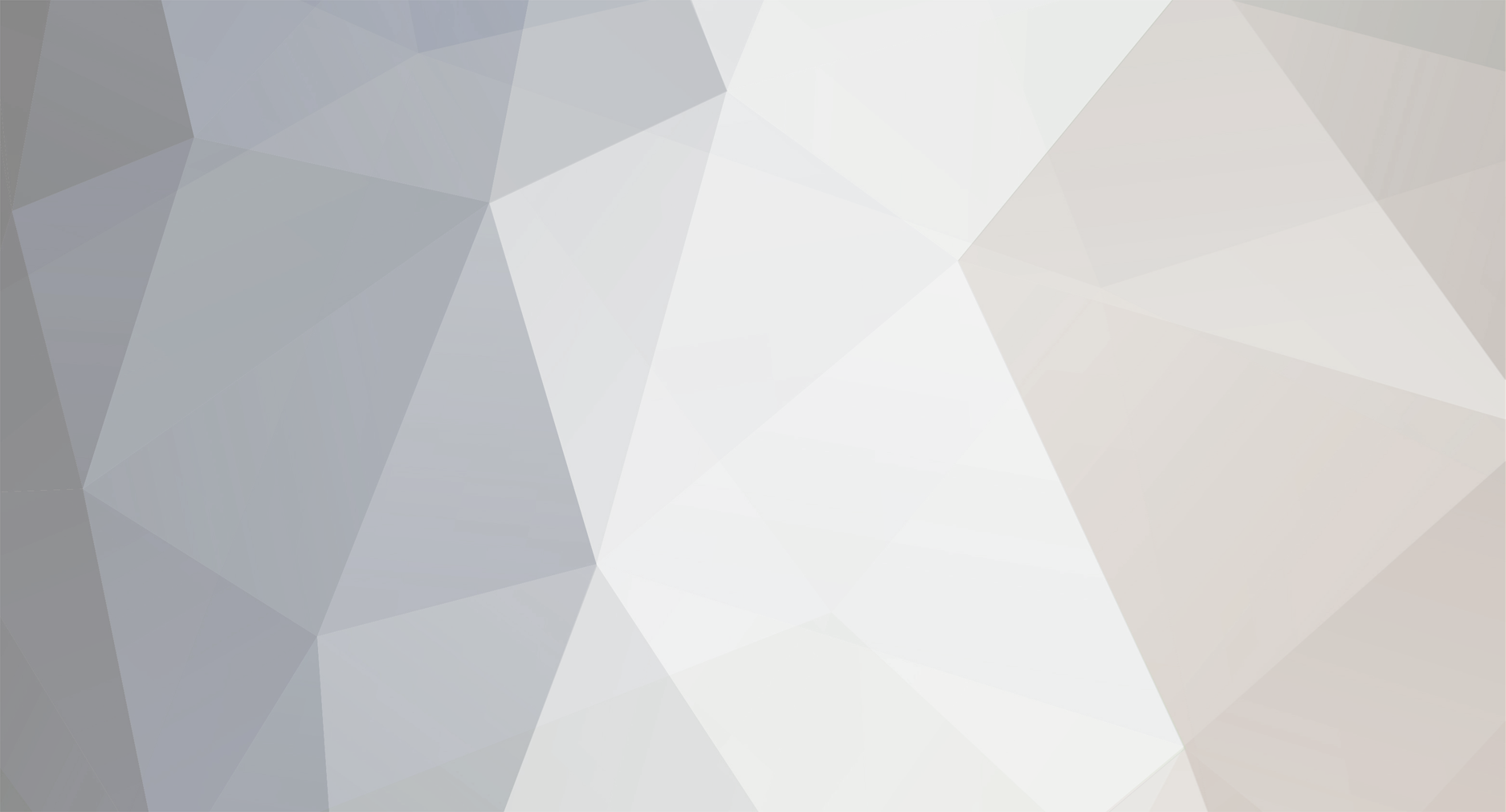
thespannerman

-
Posts
143 -
Joined
-
Last visited
Content Type
Profiles
Forums
Events
Store
Community Map
Everything posted by thespannerman
-
Having the same problem on my series 3a today. Past its MOT last year with a caution on play in front wheel bearing/ top ball joint. Have fitted a new wheel bearing (fast line, motor parts direct), still felt some play while in bench vice. Changed the top transit drag link aswell. Just got it bolted back together and the play feels the same as before I started. I do have a new sierra lower arm in stock to try? Now I can feel some play in osf, about the same as last MOT in near side front. Going to get a big bar and check for play in lower ball joint. Internet searches say wheel bearing play is a known prob on sierra? Outer races are fully seated, if not it would reduce play. torqued up with 3/4 inch breaker bar as tight as poss. Please comment. May take the hub off again and run it by my MOT tester on Monday. Bearing play can't be adjusted, set by bearing tolerances. Would a bearing kit from Ford be better? Or just the same in a different box at twice the price? Sorry for rambling
-
When your dash lit up, was the indicator switch left on? Maybe powering up the dash in reverse through the flasher relay contacts and or the indicator switch. Need to look at the wiring diagram to see if a diode or two will cure it? The spanner man
-
You can silver solder the filter back on with a plumber butane torch. Modied mine with the bottom of sump chopped off to measure gap, other wise take carfull measurements from sump/block mating surface plus gasket. I believe if the gap is too close the pump can suck air in through its mounting surface or pick up pipe gasket (not good!!). Theres a guide on NW Hoods if you search.
-
Need to fit the grease nipple in the top suspension arm tube, that the rocking pivot shaft runs through the middle of. Find a couple of grease nipples then drill where you can get your hand drill into in said tube, to a smaller drill size that you can then tap to the thread of the grease nipples. The pivot shaft runs in plain nylon bearings, so by packing the space between them with grease (till its squirts out front and aft), helps to increase there service life. The spanner man
-
For SVA on my 3a I used motorbike mirrors bolted down through the demister vents. Centre mirror was from Halfrauds; curvey asymetric shape with stickey pad fixing, sold as a mirror to watch your kids in the back. Look in Complete Kitcar, Adam Wilkins uses the same centre mirror on his Sylva Riot.
-
Took my 5 year old camping at stoneleigh and newark last year, he can't wait to go this year. Been talking about live bands and hog roasts.
-
My old engine mounts were letting the engine swing all over the place. The alternater was hitting the steering shaft. Got some engine mounts from CBS, bolted them through a piece of 3mm plate with 3 holes drilled in to match up with 3a box mounts (mounts available in different thickness). Next problem, the originals are M12 where as new ones are M10 with too short a length. Had a cut off high tensile M10 bolt welded on to increase length, then slipped on a short piece of brass tube to bring the OD back to 12mm to suit the original mounts that bolt to the side of the block. The engine is now solid mounted in the exact original position. PS had them welded proffesionally !!
-
Heat up the calliper around the nipple not the nipple itself. Hammer onto the nipple a deep socket, see what imperial or torx sockets you have to jam it solid. Keep heating, if it starts to move keep working it in and out the tiny amount until it starts to move. I always remove my nipples, clean the threads and apply some red rubber grease to the threads when bleeding. (red rubber grease is compatible with brake fluid, you can use it to lube piston seals when rebuilding callipers.)
-
As a youth I was racing along the local beach on my bike splashing through the puddles after the tide had gone out. Untill I found someone had been bait digging. Lost the front wheel to axle hight, and did a coplete forward role with my feet still clipped in. Got the front wheel of my racer crossed up going flat out along a deep JCB tyre rut, needed stiches for that one. Also done the frozen knee stop on a motorbike and the got my boot laces caught round the foot peg. LOL. Spanner
-
Used to require captive nuts for SVA. But GBSC never have captive nuts on there show cars. I have welded on captive nuts with nyloc nuts as lock nuts onto clip on eye bolts, never come undone. SVA used to say that when the main belt retaining bolt was removed the fixing plate should not fall away from the mounting point (comercial belt mount plates ussually have a small hole for a rivet or bolt to secure them to a monocoque.
-
Nice photo of your finger? Are you a Gurka by any chance? Cos they have to draw blood every time they pull their knife too. I split pvc pipe to cover the loom, cuts very easily if you draw the blade away from the pipe not trying to cut down onto it.
-
Back in the days of SVA. I put on so much foam, tape and edge trim, the tester didn't bother to get his balls out!! Happy days. Do IVA testers play fair? or are they so strict now that they are losing the point of the test?
-
Swap the bulb/light units over and see if the fault changes sides.
-
Has it finished yet? Just woke up. Watch the Moto GP next weekend for some actuall racing - they even over take each other!!
-
An overide switch on the dash for the cooling fan is a good idea. Hope to see you at Newark (clean mk2 with no screen?)
-
I use ABS plastic (carbon look) cycle wings from SVC. Alot lighter than GRP and wont crack, think I paid £76 a pair in 2007.
-
With my mild steel ones you can hammer the inside of the curve and the outside stays smooth aslong as supported properly on round bars.
-
Had the same prob, you cant buy new early engine mounts. So I measured the height of the original mount, then bought some engine mounts from CBS (various heights available). so the new engine mount plus a piece of 3mm plate gave the same height. Piece of 3mm plate on top of engine mount turret, two holes as original mount to bolt it down and hole in the middle to bolt the new mount through. Next prob is original mounts had a long 12mm stud, can only get short 10mm new ones. So I had a cut off high tensile 10mm bolt welded on to make it long enough, then sleeved it with a piece of brass tubing to make the OD back to 12mm for the engine bracket. Went to all this trouble because my original mounts were squashing, the sump was denting the engine bay floor on bumps and the alternater fins were hitting the steering shaft on left handers. Now the engine is rock solid, gives alot more confidence knowing the lump up front isn't swinging all over the place!! Have the studs welded by proffesional dont want them to snap off!!
-
Kevin, If you tig it together you can't access the screws to dismantle the frame. So if you needed to replace the glass you'd have to grind all the welds off. Some people weld a U channel to the pillars that the frame slots into.
-
Take care when fitting as it has a tapered thread. There is no sealing washer under it as it simpley jams itself up in the thread (leaving a gap between the switch and the engine block).
-
GBSC had some thicker gauge alloy ones at Newark last year. May be easier to shape and bend. Basic idea is to shape the triangle part to the body side (repeatedly hit with ball piene hammer while supported across two bars - keep working to a nice curve), then put a crease in where the curve part meets the straight upper section. Finally when held in position on body sides they will splay out to the rear, so the upper post needs to be twisted back to keep the two post parrallel with each other.
-
I just cut a hole in the side of the tunnel. P clipped the cable in a nice curve under the carpet and back up the side of the gear box cover to the clocks. Simples cost £0.00
-
If your engine is in bits why not have a full engine balance. Had my crank, conrods, pistons and flywheel done as a whole on a pinto. Good balance pays dividends on a pinto (took the weight out by grinding the big end caps).
-
Save your self a small fortune by doing the measuring and cutting your self. Cut the bottom off my sump and bolted it to the block with gasket. Took strainer off pick up pipe with gas bottles at local garage, then bolted it back to the oil pump. With a straight edge across the sump I cut the pipe down and had it silver soldered. Checked it again for pick up clearance. Cut out a box for extra oil capacity (from scrap) and bent it up. Took it to my local welder, welded the box on the side then plasmer cut a piece of 3mm plate and welded to the bottom. Might take some time but you are hard up hoodies? Total cost £15 for welding.
-
Thanks for the info, already fitted grease nipples. Cheers Spanner